Pipeline Welding Inspection: Safeguarding Pipelines with Precision and Knowledge
Pipeline Welding Inspection: Safeguarding Pipelines with Precision and Knowledge
Blog Article
Advanced Methods in Pipeline Welding Inspection: Technologies and Technologies for Improved Accuracy and Integrity in Weld Analysis
The landscape of pipe welding inspection is undergoing a significant transformation, driven by advanced techniques that promise to boost both precision and dependability in weld evaluations. Advancements such as automatic evaluation systems and progressed imaging modern technologies are redefining traditional methods, while non-destructive screening techniques make certain material stability is maintained.
Significance of Weld Evaluation
Guaranteeing the integrity of pipeline welds is vital to the general security and dependability of industrial systems. Extensive evaluation of welds is important to the lifecycle of pipe infrastructure.
The importance of weld examination extends beyond plain conformity with governing standards. It works as an aggressive action to determine and rectify imperfections, such as insufficient blend, porosity, or fractures, before they escalate right into severe problems. Effective examination strategies likewise add to the long life of pipelines, decreasing upkeep prices and improving operational performance.
Moreover, extensive weld evaluations foster trust amongst stakeholders, consisting of regulatory bodies, investors, and the communities offered by these pipelines. By ensuring that all welds meet the called for standards, companies can minimize threats and maintain their reputations. In summary, weld inspection is crucial not only for functional integrity yet also for the more comprehensive implications it holds for safety and security and environmental stewardship.
Automated Inspection Solutions
The integration of computerized evaluation systems in pipeline welding has actually transformed the strategy to guaranteeing weld top quality and integrity. These systems utilize innovative robotics and expert system to perform evaluations that are not just much faster but likewise extra consistent than conventional approaches. Automated systems can cover extensive lengths of pipelines successfully, capturing data that human examiners may overlook due to tiredness or ecological problems.
Among the key advantages of automatic assessment systems is their capacity to run in hazardous environments, decreasing the danger to human assessors. They make use of numerous non-destructive screening (NDT) strategies, such as ultrasonic screening and magnetic fragment inspection, to assess weld integrity without compromising the framework. The information collected is refined in real-time, permitting prompt responses and punctual rehabilitative activities when flaws are recognized.
In addition, automated systems promote the standardization of examination procedures, making certain that each weld is reviewed versus constant requirements. This not just boosts the dependability of outcomes but also streamlines compliance with governing criteria. As sectors remain to prioritize safety and operational performance, the function of automatic evaluation systems in pipe welding will most certainly increase, leading the way for a lot more advanced quality guarantee techniques.
Advanced Imaging Technologies
Often employed in modern-day pipeline welding inspections, progressed imaging innovations have dramatically boosted the capability to spot and analyze weld issues. Methods such as digital radiography, calculated tomography, and thermographic imaging provide assessors with high-resolution images that disclose sub-surface defects and structural variances that may be invisible to the naked eye.
This leads to quicker inspections and boosted accuracy in identifying important defects. Calculated tomography, on the various other hand, supplies three-dimensional imaging, allowing inspectors to picture intricate geometries and analyze the integrity of welds from numerous angles.
Thermographic imaging uses infrared technology to spot variations in temperature level, identifying areas of potential weakness or stress within the weld. These advanced imaging innovations not only enhance problem detection prices however likewise minimize the moment and resources required for pipeline description inspections. Consequently, they play an important function in preserving pipeline safety and reliability, ensuring conformity with sector standards while reducing functional risks.
Non-Destructive Testing Methods
Utilizing numerous strategies, non-destructive screening (NDT) methods are vital in pipeline welding inspections, permitting the analysis of weld stability without jeopardizing the material's architectural stability. NDT encompasses a series of approaches, including ultrasonic testing (UT), radiographic screening (RT), magnetic bit screening (MT), and color penetrant testing (PT) Each approach has distinctive benefits and applications depending upon the certain requirements of the examination.
Ultrasonic screening uses high-frequency sound waves to detect inner defects, providing accurate measurements of weld thickness and honesty. Pipeline Welding Inspection. Radiographic testing utilizes X-rays or gamma rays to generate photos of the weld, disclosing internal issues that may not be noticeable on the surface. Magnetic bit testing is reliable for discovering surface area and near-surface stoppages in ferromagnetic materials, while color penetrant screening highlights surface splits by utilizing a tinted color
Incorporating these NDT techniques right into pipe welding assessments enhances the accuracy and integrity of weld assessments, making sure that possible failures are determined early. As markets require higher requirements for safety and security and efficiency, the role of NDT in preserving the honesty of bonded structures continues to be essential in pipe construction and maintenance.
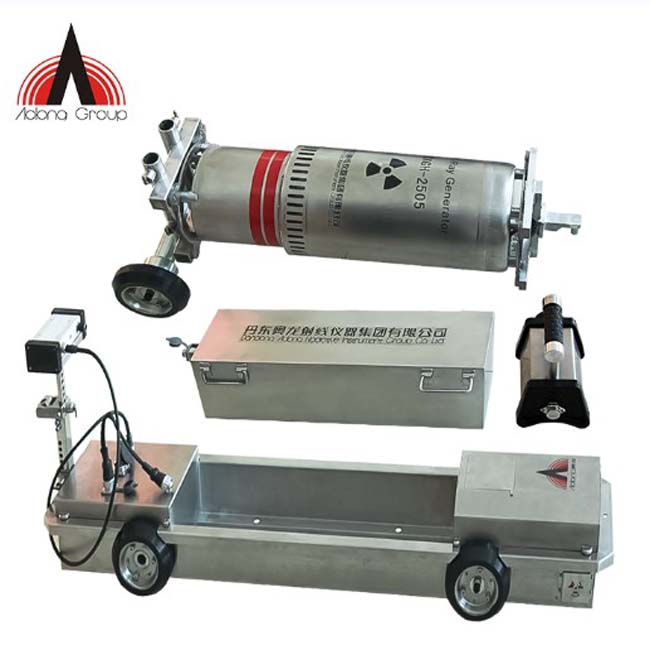
Future Trends in Weld Assessment
As we aim to the future of weld evaluation, advancements in modern technology are positioned click for more to transform the approaches utilized for evaluating pipe stability. The assimilation of expert system (AI) and artificial intelligence in examination processes is anticipated to improve the accuracy of problem discovery and predictive maintenance. These innovations allow for real-time information analysis, allowing inspectors to determine potential problems prior to they escalate right into significant issues.
In addition, the use of drones furnished with innovative imaging systems is getting grip. These aerial assessments can cover vast areas swiftly, catching high-resolution photos and information that can be evaluated for problems in hard-to-reach locations. This not just improves security yet also raises performance in the assessment procedure.
In addition, the growth of wise sensors installed in pipeline systems uses the potential for constant surveillance. These sensing units can detect adjustments in stress, temperature level, and resonances, giving useful understandings into the wellness of the welds over time.

Final Thought
Finally, the assimilation of sophisticated strategies in pipeline welding inspection dramatically enhances the accuracy and integrity of weld evaluations. Developments such as automated evaluation systems, advanced imaging modern technologies, and non-destructive screening methods play a critical duty in boosting issue detection prices and cultivating aggressive upkeep strategies. As these modern technologies proceed to evolve, they will even more make sure the safety and effectiveness of pipeline systems, inevitably adding to the integrity of crucial infrastructure.

Report this page